More manufacturers are turning to systems that combine multiple operations to shave time from part production and become more profitable. The increased prevalence of multi-tasking machines means there is also need for new tooling.
One refined and enhanced tool that facilitates multi-tasking is an innovative “peel and thread” holder that both tapers and threads in one simultaneous pass on a turning machine.
It works by incorporating a turning insert followed by a threading insert, both within the same holder. While each of the tool’s operations is relatively simple, performing them simultaneously offers several benefits.
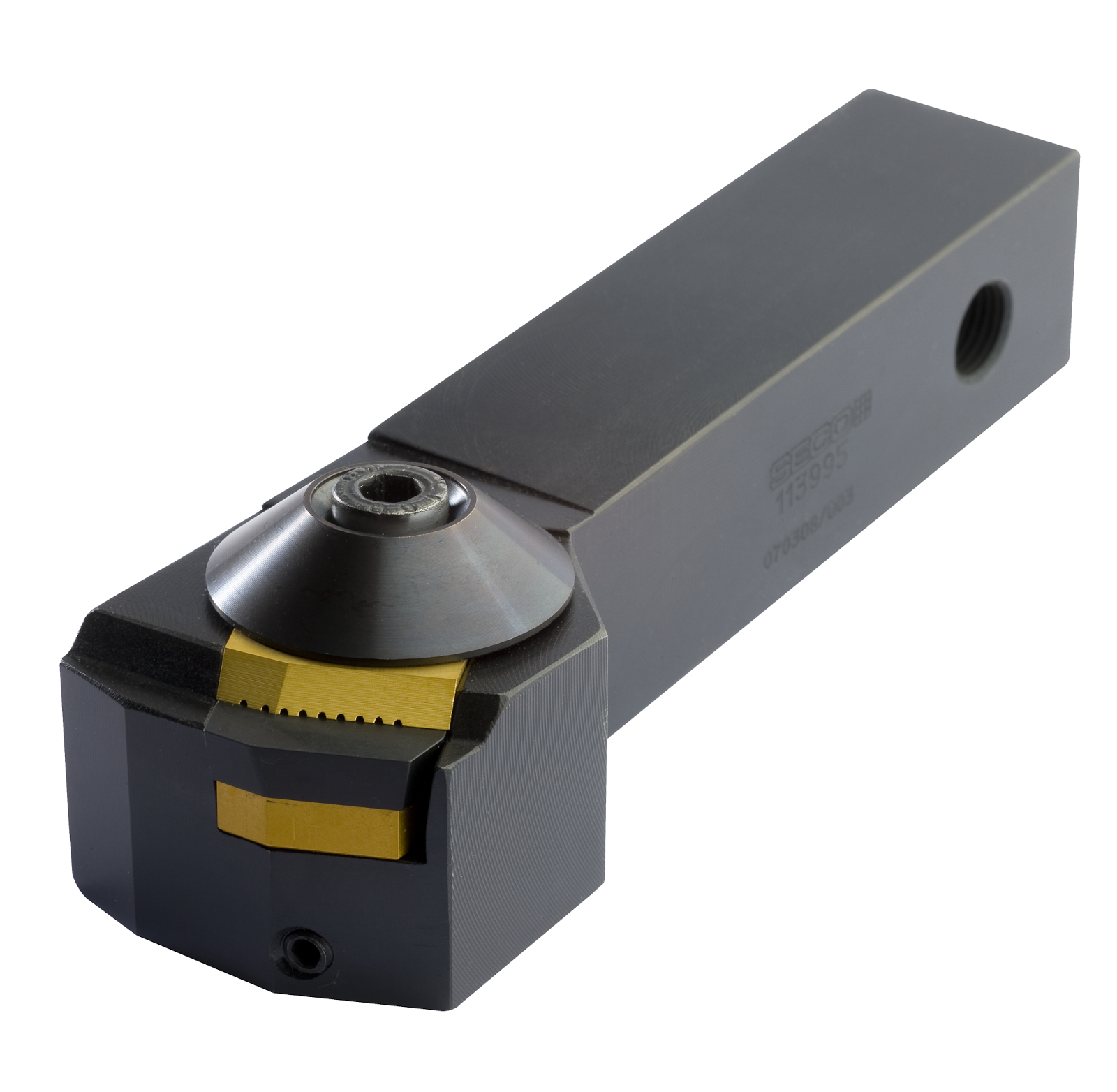
1. Shortens Cycle Times
Conventional methods of tapering and threading pipe and couplings are time-consuming. They involve first turning the taper followed by cutting the threads. The peel and thread process, on the other hand, performs both ID and OD threading. Peeling is mainly used to create the slight tapers needed when processing parts that require tapered threads. Tapered threads create fluid-tight seals, while straight threads often fail to pull mating parts together tight enough to prevent leaks.
Our peel and thread holder reduces the number of passes necessary to finish tapered pipes and couplings, so it shortens cycle times by up to 30 percent when compared with traditional separate turning and threading. As proof, a Seco customer that produces between 10,000 and 12,000 couplings daily was able to increase production by 20 percent after switching to peel and thread technology.
2. Optimizes Chip Evacuation
Chip control can be an issue when threading due to the direction of chip flow. In conventional turning and threading machine programs, the tool moves toward the chuck, which tends to deposit chips in the tool path and can easily damage the finished piece.
Peel and thread programs reverse the cutting direction. The tool starts cutting threads close to the chuck and moves away from it as the threading pass progresses which effectively directs chips away from the cutting zone and into the bed of the machine.
3. Facilitates Lights-Out Threading Operations
Better chip control that results from using a peel and thread strategy opens the door for lights-out threading operations. It also eliminates the need for manual intervention, which improves safety on your shop floor.
The only additional hardware required is the holder itself. Beyond that, you simply must apply extremely fast feed rates – typically 0.15 inch per revolution – or keep the same feed rate as threading, because you will essentially be using a finishing operation as opposed to a roughing one.
The innovative “peel and thread” holder that both tapers and threads incorporates a turning insert followed by a threading insert, both within the same holder.
Peeling is mainly used to create the slight tapers needed when processing parts that require tapered threads.
Tapered threads create fluid-tight seals, while straight threads often fail to pull mating parts together tight enough to prevent leaks.
Previously featured on SECO Cutting Edge Conversation Blog.
Talk to Us!
thank you for your forum/blog
domains for sale
42Leave a reply
Your email address will not be published. Required fields are marked *