Gripping Torque: The Answer to the Wrong Question.
Part 2 of a 2 Part Series
(see Gripping Torque: Is This the Right Way to Measure Tool/Toolholder Effectiveness?).
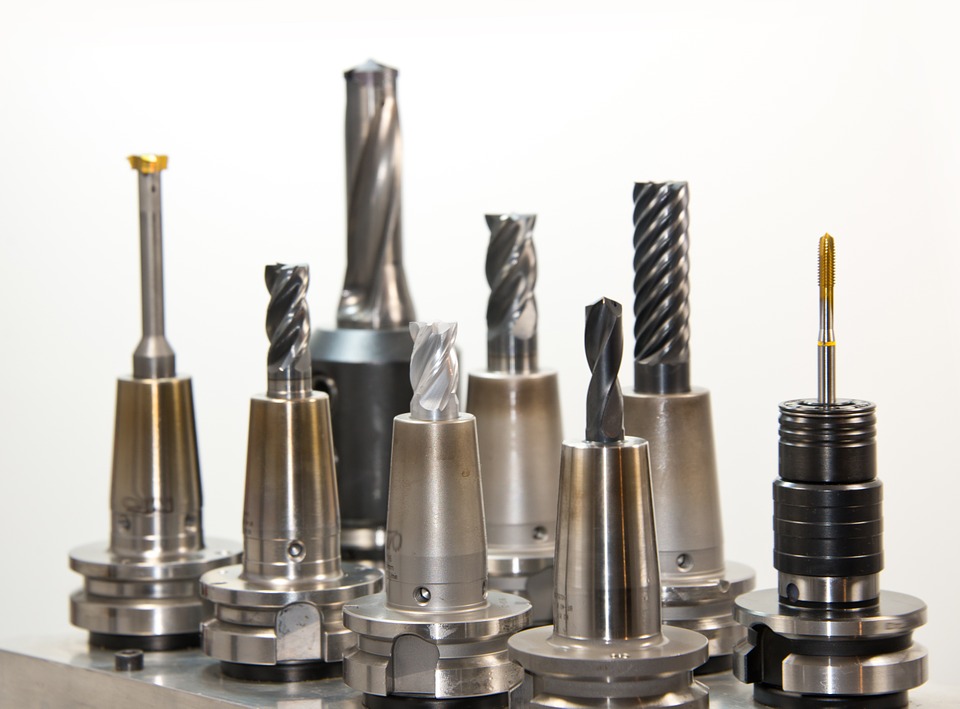
As machines for metalworking evolved, becoming faster and faster, the quest for what we call “tool security” has continued as well. As new forms of toolholders came into use, gripping torque continued to be the preferred method of judging and comparing different methods to keep tools in place for the best productivity.
Sidelock End Mill Chucks
The sidelock chuck was an early (nearly 100 years ago) solution to ensure the security of the tool. This interface involves tightening a screw on the side of the holder in conjunction with a ground flat on the side of the tool. While tool security is assured, the form fit solution creates a host of other problems that make it a less than ideal system for modern machining methods.
First, the nature of one-sided clamping via a set screw creates an obvious concentricity issue. As force is applied near the bottom of the shank, it causes the cutting end of the tool to move in the opposite direction; hence a runout problem occurs that decreases tool life and dimensional accuracy. Second, the screw on one side of the holder coupled with a cutting tool missing a hunk of material from one side creates an obvious unbalance issue. The result is increased vibration that impacts tool life, finish and spindle bearing life. The common solution to overcoming both of these drawbacks is slower speeds and feeds in order to improve life, finish or machining sound. The ultimate detriment in the end, often never realized since many machining processes are inherited, is decreased productivity.
As mentioned in our previous article, sidelock chucks are still being used today, in part because they offer a measure of tool security. However, their inherent lack of runout accuracy and balance led to the evolution of the equally popular collet chuck system. But what this system gained in accuracy, it gave away in tool security.
Collet Chucks
Collet chucks evolved from the need for greater accuracy that that of the traditional side lock holder. In this respect, the mark of accuracy was greatly improved. Furthermore, the versatility of the design was another tremendous attribute, reducing the added cost of an entire new holder when a different tool diameter was required. The improved versatility and accuracy made this chuck arguably one of the most popular tool holding methods in the industry. However, what the collet chuck gained in accuracy, it lost in gripping torque. The mechanical nature of this solution made tool pullout a real problem for those that tried any type of heavy milling operations with it. Many operators would try to compensate by over tightening the nut, but alas this only resulted in loss of runout accuracy and tool security that was still insufficient. Thus, further advancement continued.
Mill Chucks
The next evolution in toolholding came in the form of mill chucks. These are a mechanical solution developed 50 years ago to provide greater gripping torque versus collet chucks (more security) with similar accuracy so that manufacturers could have a collet-like system capable of rough milling. Mill chucks were considered superior to the sidelock in that they provided improved accuracy with enhanced gripping torque for improved security…if clamped properly. The increase in accuracy came from the collet interface, which gripped evenly 360° around the shank of the cutter while the bearing race provided increased torque transmission during tightening. Additionally they can be sleeved down, limiting the number of different holders needed for each tool diameter.
However, mill chucks have a lot of separate components. As previously noted, the tool is gripped using a roller bearing cage, which is then tightened with a large outer nut to compress the chuck around the tool. While the gripping torque is increased significantly over that of a collet, the sheer size of the roller bearing cage requires a large nut to house them, hence a holder profile that is very bulky and has poor reach capability.
Also alluded to before, is the effectiveness of the mill chuck being very dependent on the operator. Proper clamping requires the nut be tightened as far as it will go and then backed off ¼ turn. This is because the bearings roll over a bit on themselves when tightened, causing runout. By backing off, you release pressure on the bearings. But many operators, due to lack of awareness, time constraints or other reasons, tend to over tighten the nut without backing off.
Another drawback of this system is that the needle bearings never locate in the same place each time after tightening, and often are rolled over each other. The result is inability to achieve repeatable balance. At lower speeds the detriments of imbalance are not always immediately visible, but as speeds are increased, runout accuracy and tool life will drop off rapidly.
Finally, the mill chuck is an expensive holding solution. Aside from the upfront cost, there is a maintenance cost to consider, as most must be broken down and greased every 6 months. Since this takes time and money, operators often skip this vital step. As a result, gripping torque decreases and runout accuracy is compromised.
Other Options
What are some other alternatives to end mill chucks or mill chucks operators have used in an attempt to achieve tool security?
Shrink fit takes the friction fit method to another level. It uses the properties of thermal expansion to accommodate high gripping torque with added accuracy and balance repeatability. It can also be used with the Safe-Lock™ system. Not only does this system have high clamping torque, accuracy and balance; it is also one of the easiest systems for operators to learn.
The press fit system uses a mechanical press to temporarily deform a collet/sleeve in order to insert a round shank tool. The holder has a slight angle matching that of the collet sleeve. A hydraulic press moving through a straight bore in the middle presses the collet and tool in together. Gripping torque is high and runout accuracy is good, but the body of the holder lacks physical mass making it less than ideal for heavy side loads, hence not appropriate for heavy roughing. Flexibility is also lacking as tools must have a certain size shank or the collet can crack. And because the system is proprietary, you become very reliant on only one manufacturer for price, stock availability and variety of offering choices.
Hydraulic chucks are good for straight vertical work (drilling/reaming), but not for milling. They use fluid under pressure to expand an internal bladder that ultimately engages the tool. It is adequate for high speed machining with low depth of cuts and cutting forces, but it is not ideal for heavy roughing or any scenario in which greater radial forces or heat are encountered. Why? The fluid in the chuck is too flexible to provide sufficient gripping torque transmission. In addition, high performance milling in some cases can generate temperatures that actually cause the internal oil to evaporate, thus causing failure. Similar to the mill chuck, maintenance is also required from time to time to ensure internal bladders do not wear too much and start to leak.
As this article shows, the search for maximum gripping torque continued for decades without any real satisfaction because the need was not being properly defined. Gripping torque was the answer to the wrong question.
- Sidelock chucks are still being used today, in part because they offer a measure of tool security. However, their inherent lack of runout accuracy and balance led to the evolution of the equally popular collet chuck system.
- The mechanical nature of collet chucks made tool pullout a real problem for those that tried any type of heavy milling operations with it.
- The mill chuck is an expensive holding solution. Aside from the upfront cost, there is a maintenance cost to consider.
Previously featured on Haimer-USA.com.
Talk to Us!
Leave a reply
Your email address will not be published. Required fields are marked *