The demand for titanium materials in the aerospace industry is rising. Experts are predicting an average increase of 20% over the next five years. This will have consequences for the manufacturing plants, since processing titanium usually requires long machine running times. Walter supports its aerospace customers with new tools and extensive knowledge of components. The aim is to manufacture titanium components cost-effectively and in a time-saving manner.
Walter supports its aerospace customers with new tools and extensive knowledge of components. The aim is to manufacture titanium components cost-effectively and in a time-saving manner.
The aircraft industry readily uses titanium for highly stressed structural components: Door frames, landing gear mounts and wing attachments – all these components typically have a high machining content, it is not unusual for the volume of swarf produced to exceed that of the finished component. This is primarily due to the fact that a large number of pockets are cut from solid forgings. Deep and shallow pockets, 5-axis pockets, triangular pockets – often with very thin walls or bottom faces; these pose a huge challenge for milling which, logically, is the machining technology for these structural components. Indexable inserts and solid carbide milling cutters help to maintain the balance here. The main focus is on process reliability since these structural components are extremely expensive. At the same time, cost pressure from the market demands high machining and productivity performance.
Typical when titanium machining, the material's low thermal conductivity and its tendency to vibrate require a very rigid machine concept as well as optimum cutting edge preparation. Dirk Masur, Component Manager Aerospace at Walter AG in Tübingen, Germany, together with his colleagues, works with titanium components and their special properties on a daily basis: "We focus on complete solutions," he explains. "This means that we coordinate all aspects, such as the tool design, CAM program and machining strategy, with the application in accordance with best practice considerations." The result is modern tool concepts which, in turn, are matched to the tasks in question, such as roughing, semi-finishing or finishing.
Last but not least, according to Masur, the development of productive and reliable strategies at Walter is based on knowledge of components which has been built up over a number of decades: "Being part of a global network is something we consider to be extremely important. Our expertise is based on intensive partnerships with focus customers, universities and machine tool manufacturers. Together, we are continually developing the machining operations for key components. This is how we ensure that we are always using the very latest technology."
In the end, the machining specialists from Tübingen provide their customers with processes which enable maximum machining volumes. The key here is to match the processes with the available machine type capacity, for example, to gain maximum output even from machines with a lower performance. "The machining operations are simulated and verified before the handover," Masur stresses, "this means that the user does not have any unpleasant surprises in terms of cost-effectiveness or process reliability."
Representative test in titanium
Since there are virtually never any real test components readily available in the world of aerospace, nor any large structural parts, the experts at Walter AG demonstrated the performance of their current tool generations on a generic component. This is made of the commercially available material Ti6Al4V. The experts at Walter designed the component with a range of typical pocket shapes which are the same as or similar to those which can be found on real components. This means that the machining results can be transferred one to one.
The plan includes a task for a quartet of tools: The M3255 tangential porcupine milling cutter, the M4002 high-feed face milling cutter (roughing operations), the Ti40 solid carbide end milling cutter and the modular ConeFit variant with Ti50 changeable head (semi-finishing and finishing operations). This is a combination, for example, when machining landing gear mounts. The coatings, as well as the macro geometry and micro geometry of the two solid carbide tools are designed specifically for titanium machining. The M3255 and M4002 milling cutters were given indexable inserts made from the new Walter WSM45X cutting tool material. The extremely tough CVD coating is ideally suited to ISO S and ISO M applications.
The following overviews show example machining rates and tool life, which could be implemented when machining pockets on a generic component:
1. M3255 tangential porcupine milling cutter / D = 50mm, z = 5 / WSM45X:
Roughing – Pocket: 10.8 x 4.7 x 2.9 inch:
vc = 130 sfm, fz= 0.006 inch, ap= 1.46 inch (2 steps), ae= 1.18 inch (concentric tool path)
The result: Machining volume: 12.9 in³/min, tool life: 70 mins (t/pocket: 14 mins)
2. Ti50 ConeFit Prototyp / D = 25mm, z = 5 / solid carbide changeable head:
Semi-finishing and finishing – Pocket: 10.8 x 4.7 x 2.9 inch:
vc= 295 sfm, fz= 0.004 inch, ap= 0.630-0.866 inch (variable), ae= 0.146 inch (semi-finishing), 0.012 inch mm (finishing)
The result: Machining volume: 2.0 in³/min, tool life: 60 mins (t/pocket: 14 mins)
3. M4002 high-feed face milling cutter / D = 50mm, z = 5 / WSM45X:
Roughing – Pocket: 10.0 x 5.0 x 1.65 inch:
vc= 60 m/min, fz= 0.028 inch, ap= 0.60 inch, ae= 1.97 inch
The result: Machining volume: 5.7 in³/min, tool life: 40 mins (t/pocket: 10 mins)
Milling with a difference: High dynamic cutting
A very good example of an intelligent machining strategy is "high dynamic cutting" (HDC). This improves both cost-efficiency and process reliability. With high dynamic cutting, the machining conditions remain constant – along, therefore, with the forces applied to the tool cutting edges and the process temperature. The corresponding functions are provided by modern CAM software. Advantages: Better performance and greater process reliability. The constant engagement condition generates lower vibration – and thus results in a higher tool life at a lower tool wear rate. This, in turn, enables higher cutting lengths and machining volumes. At the same time, energy consumption at the spindle is reduced. The Walter Prototyp Ti40 solid carbide milling cutter is perfectly suited to this machining strategy.
4. Ti40 Prototyp / D = 20mm, z = 5 / solid carbide end milling cutter for titanium materials:
High dynamic cutting, triangular pocket: 7.87 x 3.62 x 1.89 inch:
vc= 380 sfm, fz= 0.005 inch, ap= 1.87 inch, ae= 0.079 inch
The result: Machining volume 8.5 in³/min (t/pocket: 9 mins)
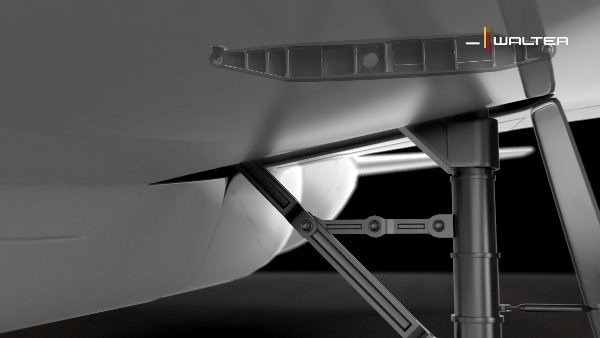
But what about aluminium?
Aluminium is an integral part of the ensemble of materials used in modern aircraft. It continues to play an important role, despite the increase in the use of composites. This is also partly because the development of new alloys with improved properties is ongoing. The current trend is towards aluminium-lithium wrought alloys.
Al-Li alloys are lighter than other Al alloys and have a higher modulus of elasticity – welcome properties for the aircraft industry. Workpieces made from these lightweight materials are often similar to those made from titanium. Both have a large number of pockets – and consequently high volumes of swarf. The main difference is that aluminium machining is a HSC (High Speed Cutting) process. There is no talk of materials being "difficult to cut" or "reduced cutting data". On the contrary – milling speeds above 10,000 sfm are not uncommon. On the other hand, cutting speeds which are too low result in the formation of built-up edges – and thus to lower tool life. In the same way as titanium machining, working with aluminium also requires a great deal of expertise and component knowledge where the aim is to develop cost-effective, reliable processes. Here too, the focus is on complete solutions matched to the application, with the tool and machine concepts optimized for aluminium.
This is why Walter AG has recently introduced a new milling cutter – an aluminium specialist through and through – which is tailored precisely to the requirements profile of the aircraft industry: The M2131 ramping milling cutter with 90° indexable inserts. Its speciality is ramping and pocket milling. Walter manufactures the milling bodies with the highest possible concentricity, with the indexable inserts having protection against centrifugal force. The milling cutter is also pre-balanced. These measures guarantee that high process reliability is achieved in HSC machining.
The highlight of the new tool is, however, the WNN15 grade indexable inserts. This refers to an entirely new PVD coating type, manufactured using the "HiPIMS method". "HiPIMS" stands for "High Power Impulse Magnetron Sputtering". The special feature of this physical coating process is that it produces an extremely resilient and smooth PVD coating. The benefit of this new variant is the huge reduction in friction – and thus less formation of edge build-up. It also provides extremely high resistance to flank wear as well as extremely high cutting edge stability. "Field tests have confirmed the technological advantages of the new indexable inserts in comparison to standard types," explains Wolfgang Vötsch, Product Manager for Milling at Walter AG in Tübingen. "Our application engineers have achieved increases in tool life of up to 200% with ease. In one case, we even succeeded in reaching an increase of almost 400%!"
For a Complete Offering of Walter Tools visit MSCDirect.com.
Talk to Us!
Leave a reply
Your email address will not be published. Required fields are marked *