The new CEO of the American Society of Safety Professionals, a former Manufacturing Institute president, talks about the organization’s role, trends in the safety profession and more.
ASSP's big annual event, Safety 2019, is upcoming June 9-12. When Jennifer McNelly became CEO of the American Society of Safety Professionals (ASSP) in August, she stepped into the lead role of the longest-running safety society in the country. With more than 38,000 members, the society serves as an advocate for workplace safety and health professionals, helping develop new safety standards and educating its members on workplace safety and health.
Jennifer McNelly is about to inaugurate her first major ASSP event "Safety 2019" in New Orleans next month. We caught up with her earlier this year about the organization and major safety education trends.
McNelly’s background in manufacturing in both the public and private sector and experience in education, job training, workforce development and standards allowed her to hit the ground running at ASSP. She works with the board of directors to execute the organization’s strategic plan and meet the evolving needs of the professional occupational safety and health community.
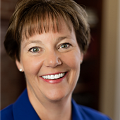
CEO, ASSP
We talked to McNelly, a former president at The Manufacturing Institute (the nonprofit affiliate of the National Association of Manufacturers), about trends in the profession, certifications, how facilities and safety managers can keep up with technology and compliance, new ASSP programs, and industry best practices.
What are some trends in the safety profession? Are there different philosophies that are coming into play?
MCNELLY: There are a couple of things that have popped up in trends as I think about the life of a safety professional. One of them is what I call systems thinking and systems management. How do we drive toward a systems-based approach, where health and safety professionals are not only about compliance—and checking the box—but are part of the larger discussion of operations?
The second is what I consider the changing thinking around individuals who show up to work every day. A lot of terms get used but the one we talk about in the building and with our partners is “total worker health.” What does that mean? It’s about mindfulness—when employees are showing up to work with a whole different set of circumstances, how are we as safety professionals preparing for that and supporting that?
The third is reality-responsive. This is where topics like workplace violence come into play. We have an active shooter technical report coming out shortly. Workplace violence and active shooters aren’t the kind of discussions that we had even just a couple of years ago. How are we preparing for that? How are we making sure our safety professionals are well-equipped?
Keep track of all this year's ASSP event coverage on our MSC at Safety 2019 page.
What’s the best way for safety professionals to stay up to date on technology and compliance?
MCNELLY: An important role ASSP plays is around professional development and making sure professionals have good information.
As a society right now, we have a board-level task force that pulls internal and external stakeholders together and has a research agenda. Based on the conversation going in the marketplace, we’re looking at gaps to see how our members are impacted, and then we’ll develop products and services in response.
We also do two really large professional development conferences each year—Safety 2019, an annual professional development conference and expo, is in New Orleans this summer, and Seminarfest is in Las Vegas from Jan. 24-31.
We are also a founding partner in the Center for Safety & Health Sustainability, which is looking at, for example, how we all collectively come together to advance the voice of the safety profession.
As a member association, we are constantly evolving our communication channels.
We have a podcast—the Tech Pubs Podcast, technically called the Safety Standards and Tech Pub Podcast—where we can put information out in the marketplace.
One of the best benefits members get is good information that they can disseminate, and one of the ways they can do that is our Professional Safety journal (PSJ).
We consider ourselves an honest broker in this space. So we want to both empower safety professionals and also support them through all of our communication channels.
What are the most popular certifications for safety professionals right now? Are businesses starting to look for certain certifications more than others?
MCNELLY: We see a lot of preparation for some certifications, like the Certified Safety Professional. We also see an increase in topical areas within learning and development.
What we have seen from our member feedback is certifications are one point in the journey. What we need to be responding to are just-in-time requirements of members. So the importance of professional development in being able to deliver in many cases a subset of the topic a certification may be about (such as workplace violence, fall protection or systems management).
Leadership development is another one of those topics. We need to constantly build our members’ technical capabilities, but more and more we’re offering opportunities for leadership development.
We had a leadership conference in October. It spanned best practices from leading through times of change to understanding employee motivation.
Need to change behavior toward safety? Learn how in “To Integrate Safety Culture, Focus on Changing Behavior.”
Are there new best practices you see being introduced for health and safety professionals?
MCNELLY: What we’re focused on as a society is really that systems approach. We were a significant sponsor/supporter of the global effort around the standard called 45001 [ISO 45001], based on the Z10 standards [ANSI Z10] here. That’s about a global approach to how you integrate to advance safety and that happens through our 38,000 members across the globe. That is one of those best practices or trends that continues.
Does ASSP have any new programs it will be introducing for safety professionals?
MCNELLY: Our foundation side of the house is working to expand safety programs and develop resources to support education institutions that want to build a pipeline of future safety leaders based on their market needs. Workforce development in general tends to be an issue.
How do we find safety professionals? How do we make sure we have quality safety professionals?
How do we constantly develop them?
Our goal is to ensure that we create a solid career pathway grounded in definitions of a safety professional.
We also have a new Certification and Accreditation Institute. This links back to that 45001 standard; the purpose behind the ASSP Certification and Accreditation Institute is to support companies in achieving that gold standard of systems integration as defined by 45001.
In a recent interview with Business Insurance, you said something interesting about the job of a safety professional is not just to try to prevent mistakes but to make sure that when (not if) they happen, the consequences aren’t as serious. Can you talk about that a little bit more?
MCNELLY: Part of my point in the Business Insurance article is that safety isn’t compliance; it’s a partnership that happens that is empowering frontline workers to have a role in this and C-suite to have a role. It’s not just about the professionals.
Our role and responsibility is to equip them to be prepared for those conversations but to also ensure good information is out in the marketplace. And that links back to a lot of our efforts around standards development.
You need to be able to demonstrate and show what good looks like, and that’s where the transparency of a standard comes into play.
What makes manufacturing organizations with a strong safety culture successful?
MCNELLY: Inherent in a manufacturing environment is process improvement. We are constantly looking at the cycles of engagement and, by nature of Six Sigma and some of the processes in place, we’re empowering front lines to bring issues forward that can be addressed.
Inherent in the culture of manufacturing is a strong safety environment because you’re always looking at all the frontline points of influence. That to me is part of what makes manufacturing great.
What best practices in safety does your workplace use?
Talk to Us!
Leave a reply
Your email address will not be published. Required fields are marked *