Tips to introduce this useful practice into your shop.
Originally developed in Japan during the 1970s as part of the radical “just-in-time” manufacturing technique, 5S is the cornerstone of lean manufacturing. The workplace organizational methodology encourages the idea that excellence can be achieved through visual order, attention to detail, cutting waste and putting everything in its allotted place.
“5S provides the foundation for effective and efficient work processes by ensuring that only the required items (material, information, tools, supplies) are in the work area,” says Douglas Jones, executive vice president of MSC Industrial Supply Co. “Once all of the nonrequired items are removed, an associate can complete their processes without having to leave the work area to locate and bring items back. This builds the discipline needed to sustain the work area and prevent unnecessary items from creeping back in.”
Want to implement 5S methodology at your company? Jones offers some advice on how to get started:
Step 1
Identify the benefits and determine to what degree your company needs to increase standards of quality by lowering costs, improving safety, decreasing manufacturing time or reducing inventory.
Step 2
Assess your culture and operations to decide how best to introduce 5S methodology and perhaps other lean concepts. Regardless of title or position, employees across various levels and functions should feel empowered to examine their individual and collective work processes to develop a strategy for implementing the methodology. Once you define what it is you are trying to achieve, tailor it for your company.
Step 3
Identify opportunities for waste reduction and efficiency gains by analyzing the amount of materials used, production time, additional movement on the floor if tools, machines and workers are improperly stationed, and the ease in the flow of information. This includes identifying the potential value and gains throughout the process. Also, don’t just copy what other companies are doing; come up with a plan that best fits your organization.
Step 4
Implement the 5S methodology and evaluate your results. How much time and money are wasted on just searching for items on the shop floor every day? Invest in storage containers, label makers and displays of your 5S audit. Not only is the objective to uncover challenges, errors or problems and create a culture where you can quickly find solutions, but also to sustain this ongoing process. Don’t let the idea of being “perfect” get in the way of being “better,” so focus on the smaller, incremental improvements first.
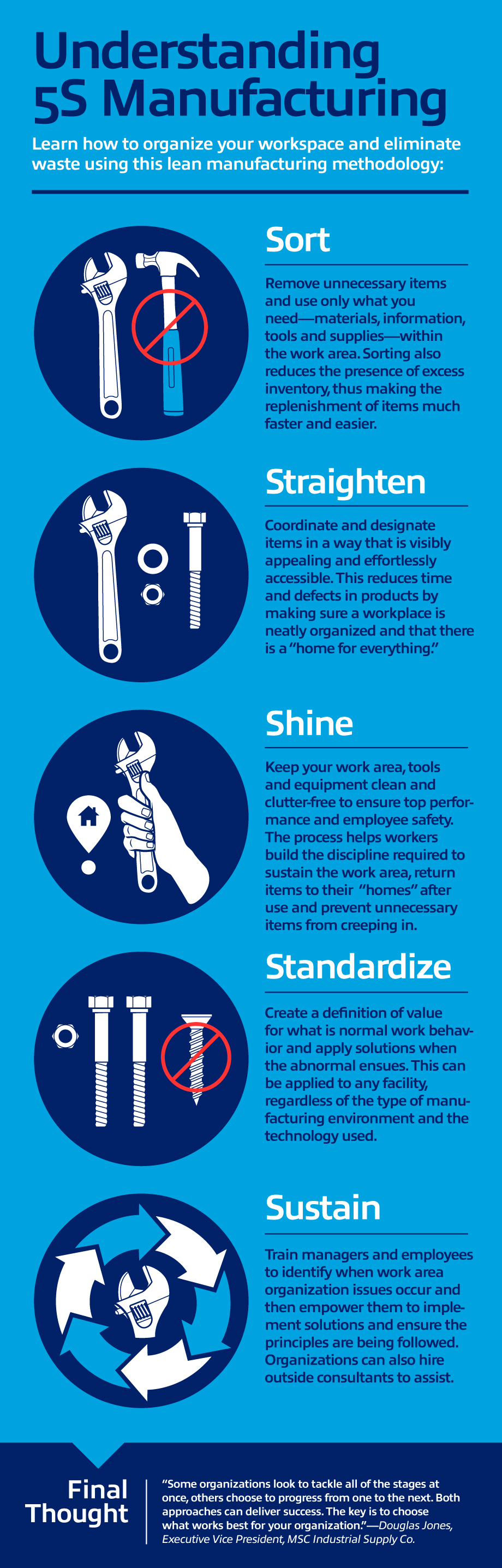
Talk to Us!
Leave a reply
Your email address will not be published. Required fields are marked *