Transforming your work culture and bottom line through lean methodology
The principles of lean manufacturing rose from the ashes of World War II, when engineers such as W. Edwards Deming and Shigeo Shingo helped Japan rebuild its industrial complex. But it wasn’t until the early 1990s, after significant results were published in the MIT study “The Machine That Changed the World,” that “lean” became a manufacturing buzzword.
Lean manufacturing is popularly understood to be a set of tools or a system used in the workplace to eliminate waste, ultimately leading to improved production and quality while saving time and money. Manufacturers all over the world over have embraced the concept, including giants such as Ford, Caterpillar, Intel and especially Toyota, which introduced the first standardized lean methodology, the Toyota Production System.
Making Lean Methodology Work at Work
While implementing a lean philosophy can be daunting, it does not require thousands of employees and billions in revenue. Lean manufacturing is, in fact, the great equalizer across employee roles. Mike Petkewich, a senior knowledge expert and team manager for lean manufacturing at The Boston Consulting Group, has helped many companies incorporate lean manufacturing and says industry still has room for improvement when it comes to systematizing and standardizing practices.
“Lean is about transforming your business culture,” says Petkewich. “Getting people to see the waste, and then giving them the tools and techniques to think differently, to reduce and eliminate that waste—that’s the key. But until you actually do the training and get everyone pulling in the same direction—including those at the top of the organization and those not directly involved in manufacturing—a lot of things will continue to be taken for granted.”
Waste is defined as something that adds no value to a product, Petkewich explains. It can be physical waste, such as a pile of scrap, or time waste, such as a machine operator waiting for a cycle to end. But it can also be something less obvious—excess work in a process or even the wasted potential in people. Lean philosophies identify these opportunities and empower people to fix them.
There are key indicators. “You know that lean is working when the shop is clean and well-organized; no one’s in firefighting mode. Everyone shares information, with clearly defined metrics, and pride of ownership,” says Petkewich. “Most importantly, they don’t stop their improvement efforts once lean has been officially implemented. They keep chipping away at problems. That’s the spirit of Kaizen, otherwise known as continuous improvement.”
Putting Lean into Action Saves Time and Money
When employees proactively work together to achieve systemic improvements to the manufacturing process, it can have powerful results. MSC Industrial Supply Co. supports customers committed to making this kind of effort with Application Optimization, a service that leverages a vast database of real-world machining scenarios to help customers analyze metalworking processes and remove waste.
The process is continuous and can include switching to different cutting tools, adjusting feeds and speeds, replacing tool holders, reprogramming a CNC machine or identifying better processes for more efficiency. The results are then validated and documented so that the information can be applied to other production operations across the shop floor. The Application Optimization service is supported by a metalworking specialist and a key account representative, as well as a team of experts behind the scenes who will identify opportunities to reduce total tooling cost per part, yet another example of waste.
Knowledge sharing, process optimization, space and lower levels of inventory are important in today’s world of rapidly evolving technology. Lean methodology is the missing piece of the puzzle that is helping manufacturers become stronger competitors in the global marketplace.
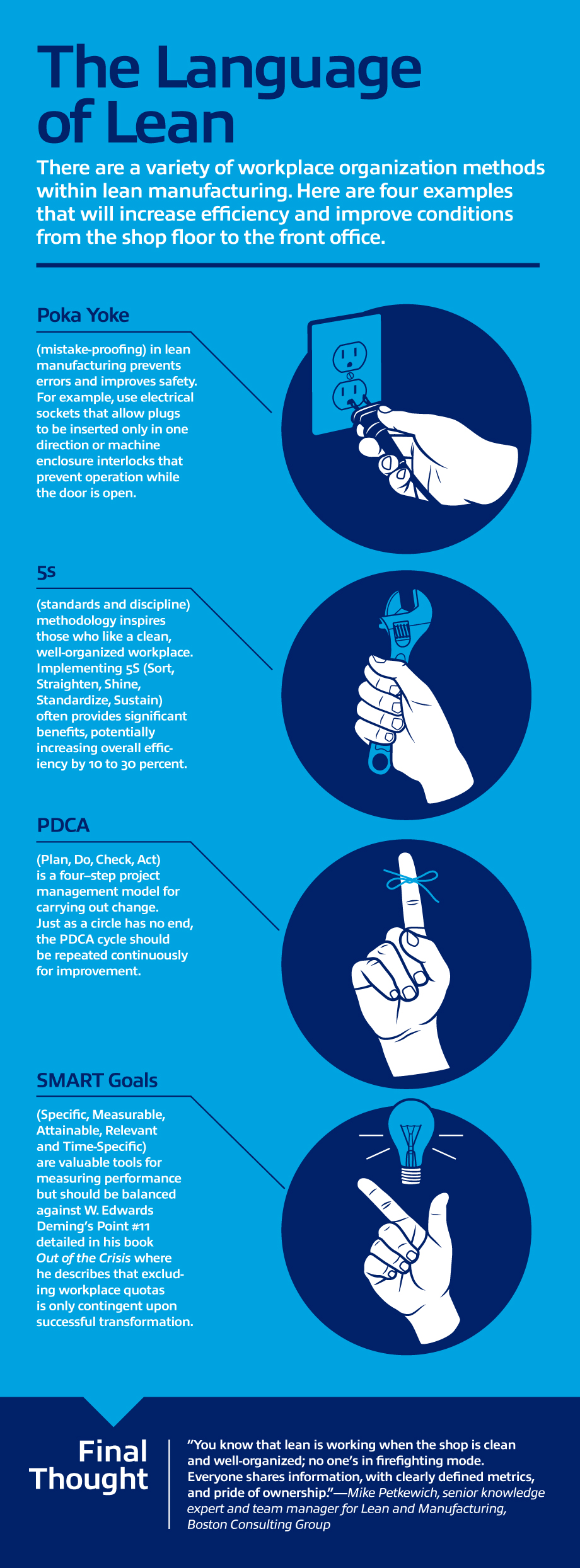
Learn to think differently about waste in the workplace.
All employees, regardless of position, require training for the lean philosophy to work effectively.
MSC’s Application Optimization service can help customers get organized and save money.
Talk to Us!
Leave a reply
Your email address will not be published. Required fields are marked *