To browse Sandvik's full line of tooling solutions visit MSCDirect.com.
Video Highlights
Chip control and chip jamming present major challenges for turning operations. It can lead to reduced workpiece quality, scrapped components, wasted material, shorter tool life, and machine stoppage. If this a primary concern for your machine shop, then watch this short video where Sandvik demonstrates proven methods to ensure quality chip control in conventional and PrimeTurning™ operations.
For a full transcript of the video, click here
Watch this short video where Sandvik demonstrates proven methods to ensure quality chip control in conventional and PrimeTurning™ operations.
Video Transcript
Chip control and chip jamming present major challenges in all turning operations. Poor chip control can lead to reduced workpiece quality, scrap component, wasted material, shorter tool life and machine stoppage, all factors that negatively impact productivity.
In this film we will demonstrate proven methods to ensure quality chip control in conventional and PrimeTurning operations. Chip control issues are particularly common within a mass production environment, where the components machined are castings or forgings.
Improving chip control comes down to four factors—the nose radius, the depth of cut, the feed rate and the top-form geometry of the insert. Many shops try to be as efficient as possible with conventional turning, using tools with large entering angles and the largest nose radius possible. This helps thin the chips, resulting in increased tool life and productivity.
However, this method makes chip breaking more difficult, leading to long, stringy chips that can wind around tools or the workpiece. Stopping the machine to manually untangle the jam greatly slows down production. Thus, using a smaller nose radius than usual can be a successful, though less conventional method. Additionally, the operator also needs to factor in the feed, depth of cut and insert selection.
Consider selecting a tool with precision coolant. Paired with an insert geometry that offers better chip breaking capability will allow you to increase both the feed and depth of cut, resulting in much higher productivity. To avoid chip jamming in conventional turning, turn towards the shoulder and stop before the dimension of the shoulder.
Maintain the same feed rate for four horizontal cuts. The final vertical cut should be done from outer diameter towards the inner diameter. The advent of PrimeTurning offers an alternative to machining mass production components. PrimeTurning begins the cut at the chuck and removes material toward the end of the component. Chip jamming is avoided as this allows for long, thin and straight chips while maintaining quality and efficiency.
As PrimeTurning starts the cut at the shoulder, it is important to always use feed reduction and a radial entry to maintain tolerances. With PrimeTurning, the direction of chip evacuation must be considered. The most efficient PrimeTurning operation involves chips breaking toward the unmachined surface, forming a roll that will break consistently. This results in superior surface finishes and operational efficiency while avoiding costly tool damage.
Brought To You By
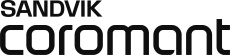
Sandvik Coromant is the world’s leading supplier of tools, tooling solutions and know-how to the metalworking industry. With extensive investments in research and development they create unique innovations and set new productivity standards together with their customers. These include the world's major automotive, aerospace and energy industries.
Related Articles
A part surface can require a specific metal finish for many reasons, be it cosmetic, product functionality, or customer preference.
Stainless steel has several common finishes. It’s important to know what these common finishes are and why they are important.
In this webinar, Kennametal shows you tips and tricks for the most efficient methods for pocket milling in aerospace applications.
Talk to Us!
Leave a reply
Your email address will not be published. Required fields are marked *